What other types of rock drills are there besides internal combustion type?
rock drills are tools used to directly mine stone. They drill holes in the rock layer so that explosives can be placed to blast the rock, thereby completing the mining of stone or other stone projects. In addition, Rock drills can also be used as destroyers to break hard layers such as concrete. Rock drills can be divided into four categories according to their power sources: pneumatic rock drills, internal combustion rock drills, electric rock drills, and hydraulic rock drills.
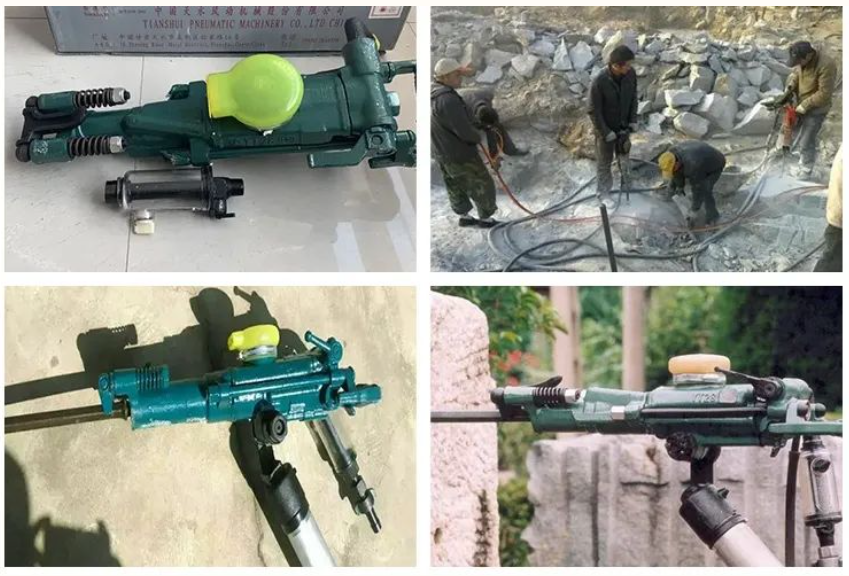
Pneumatic rock drills
Pneumatic rock drills use compressed air to drive the piston forward in the cylinder to make the steel drill hit the rock, and are the most widely used.
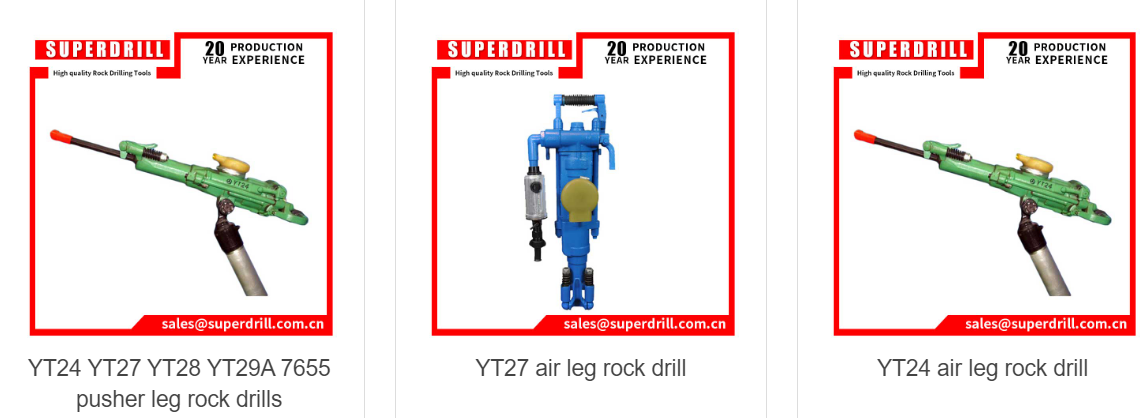
Electric rock drills
The electric type uses an electric motor to drive the hammer head to impact the steel drill through a crank-connecting rod mechanism to hit the rock. The powder discharge mechanism is used to discharge stone chips. The internal combustion type uses the principle of an internal combustion engine to drive the piston to impact the steel drill and hit the rock through the explosive force of gasoline. It is suitable for construction sites without power and gas sources.
Hydraulic rock drills
Hydraulic drills rely on hydraulic pressure to impact steel drills through inert gas and impact bodies to drill rocks. When these rock drills are impacted, the rotating drill mechanism forces the steel drill to rotate the angle, so that the drill head changes its position and continues to drill the rock. The piston is driven by the explosive force of diesel to impact the steel drill, so that it can continuously impact and rotate, and the stone chips are discharged by the powder discharge mechanism to drill a blast hole. As one of the important engineering equipment, hydraulic rock drills are indispensable in engineering construction in the fields of mines, roads, and buildings.
However, while the rock drill industry is constantly developing, the domestically produced hydraulic rock drills are still in low efficiency, some structures and parts have short service life, and there is no vibration reduction device during the working process, which causes large vibration and low energy transfer efficiency.
Internal combustion rock drills
Internal combustion rock drills do not need to replace the internal parts of the head, and can be operated by moving the handle as required. It is easy to operate, saves more time and effort, and has the characteristics of fast drilling speed and high efficiency. When drilling holes in rocks, it can drill vertically downward and horizontally upward at less than 45°, and the deepest hole can reach six meters. Whether in high mountains or flat land, whether in hot areas of 40° or cold areas of minus 40°, this machine has a wide range of adaptability.
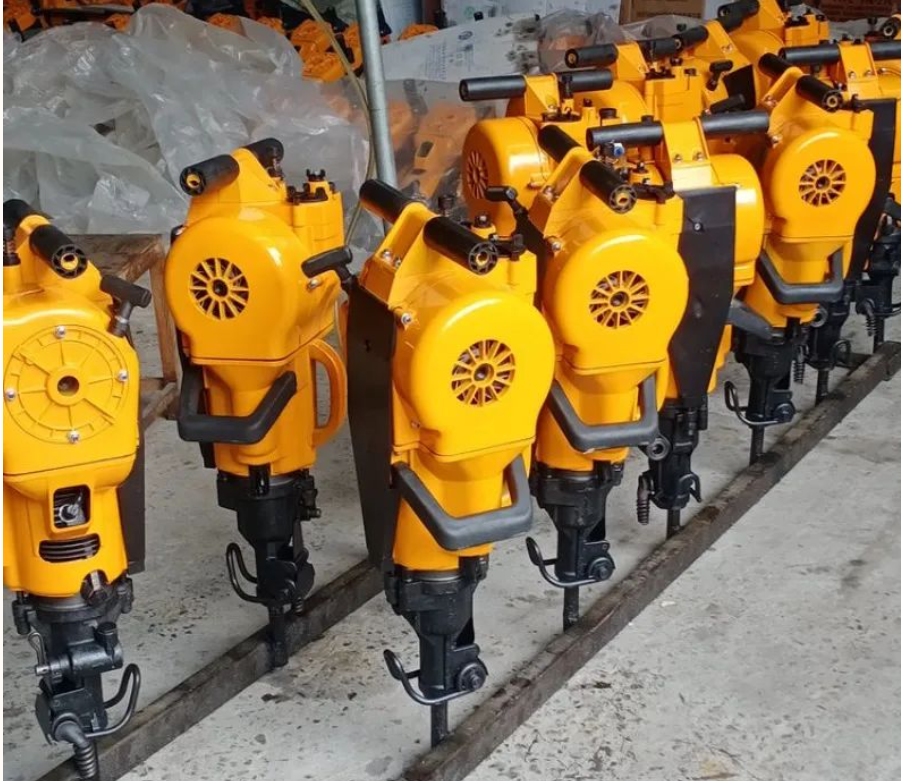
Internal combustion rock drills have various functions such as splitting, crushing, tamping, and shoveling in mining, construction, cement pavement, asphalt pavement, etc. They are widely used in mining, construction, fire fighting, geological exploration, road construction, quarrying, construction, national defense projects, etc.
Maintenance of rock drills
Ensure the cleanliness of grease. During normal work, ensure that maintenance personnel, tools, and spare parts are absolutely clean. In production, strictly implement the online oil filtration cycle and test cycle of oil products, strictly perform offline maintenance and repair according to the equipment use cycle, strictly implement the point inspection system (for faults found during the inspection process, the accident will be handled in the bud at the first time to avoid the expansion of the accident), strictly implement the tripartite agreement, strictly implement the fixed repair system, and do maintenance first and repair later to ensure zero accidents in production.
Internal leakage of rock drills
Due to the high position and high frequency of action, the internal seal of the rock drill has a short service life. Therefore, strict requirements are placed on the internal sealing of the rock drill, and strict requirements are placed on the use of high-temperature resistant and tough seals, such as rubber. Once the rock drill leaks, it must be replaced, which will directly affect normal production.